Waiting NVA: See It, Eliminate It!
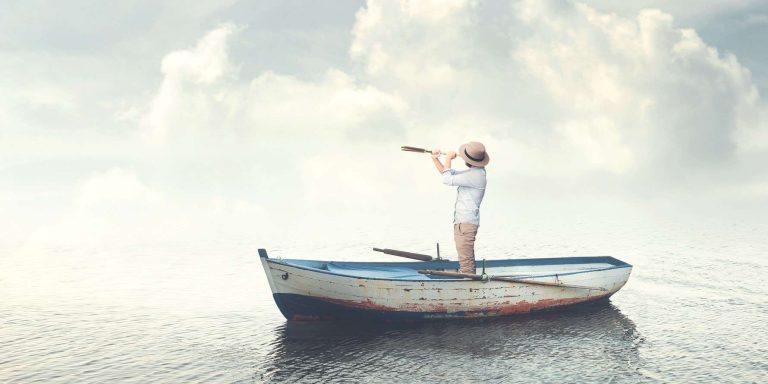
Two of the more difficult to discern and difficult to correct types of non-value added (NVA) activities are Waiting and Motion. Part of the reason is that, at first blush, process owners and operators tend to view them as “just the way it is,” not as a problem to be solved.
However, as we find with other types of NVA, the crux of the issue is that Waiting and excessive Motion have the effect of slowing the creation of customer value in the process. They add more implicit costs, and thus it is worthwhile to understand them and work to reduce or eliminate their causes. (The 8 types of NVA are described here.)
We’ll explore Waiting here, and Motion in a companion piece.
What's Wrong with a Little Waiting?
In an assembly process, a quantity of product may be waiting in front of one or more workstations due to a worker shortage, a machine breakdown, a component shortage, or some other unplanned condition. Waiting can also result from overproduction at upstream processes because of the perceived efficiency of keeping the upstream worker or machine “busy.”
Waiting does not just affect manufacturing processes. Product development can also be adversely affected by Waiting NVA. Have you had the experience of building engineering prototypes of a new design and finding that a key component has a 12-week or longer lead time, even for sample quantities? The long wait severely disrupts an aggressive development schedule and usually leads the project manager to perform other NVA activities to work around it.
Waiting NVA is an indication that process operation cycle times are not balanced, or project activities’ task times were delayed and not recovered, or were not properly planned.
How Do We Eliminate Waiting NVA?
I said at the outset that it is often difficult to discern and difficult to correct Waiting NVA. It’s not impossible, though.
Consider the manufacturing process metrics of takt time and cycle time. Takt is the German word for ‘pulse,’ and is the rate at which the line must produce units to meet demand. Cycle time is planned and measured for each operation in the line. It is the time required to complete the operation.
If every operation can be performed in less than the takt time, then demand can be met. If all operations have the same cycle time, the line is said to be balanced. If cycle times vary, the line is not balanced, but can meet demand only if all cycle times are less than or equal to the takt time.
Let’s look at an example.
An assembly line 2-shift workday has 15 hours of labor and tool time available. The daily customer demand is 300 units. Then the line needs to produce 300 ÷ 15 = 20 units per hour.
The resulting takt time is 60 minutes ÷ 20 = 3 minutes for the line to exactly meet daily demand. This means every 3 minutes, an assembly unit should move from each operation to the next, and a finished product comes off the line.
Suppose, however, the 3rd operation (Op #3) in a sequence of 12 operations requires 4 minutes to perform. Then in the 15-hour workday, Op #3 will only be able to produce 225 subassemblies. Downstream operations will be starved for work-in-process (WIP) every day, waiting for units to continue processing, and the overall line output will be limited to 225 per day.
This is actually a common line problem, especially during a demand growth phase; if demand had been 200 per day and is then increased to 300 per day due to higher sales than forecast (Hooray!), this Waiting NVA problem will be exposed and will need to be addressed.
A brute force solution could be tried, such as to:
Push the workers at Op #3 to work faster; or
Extend the workday for Op #3 to produce the additional 75 units (~5 hours); or
Add weekend time for Op #3 to catch up and build ahead.
These brute force changes may seem to work. However, they lead to other types of NVA, including overproduction, inventory buildup, and a high potential for defects and extra processing. These supposed solutions are worse than the Waiting problem.
Instead, consider a Lean Six Sigma approach to the imbalance and resultant Waiting NVA, especially if the higher demand is expected to continue or even to increase further.
How? If you don’t already have it, create a process flow diagram, or at least a table of operations with their cycle times and hourly or daily capacities listed.
Examine in detail the highest cycle time operation (Op #3 in our example) and determine if it can be reduced below takt time, perhaps by performing some of its tasks in the previous or next operation.
You could decide to add another daily shift. This option would increase available time per workday from 15 hours to, say, 21 hours. Required hourly units would then be (300 units ÷ 21 hours) = 14.3, and the resultant takt time would be (60 ÷ 14.3) or 4.2 minutes. The Op #3 cycle time of 4 minutes is less than the 3-shift takt time and would meet the required daily output.
Another alternative for the high cycle time at Op #3 might be considered instead, such as:
Add a second workstation; or
Split Op #3 into two parts, #3a and #3b; overall line 13 steps instead of 12; or
Other possibilities considering their impact on labor cost, tooling cost, and tool acquisition time.
Good Start - Now Keep Going!
The ideas explored in this brief introduction to Waiting NVA are examples of the techniques called PDSA, Kaizen and Heijunka. In essence, we are looking for ways to bring about improvements to achieve higher performance in our production line, development project, or other business process.
PDSA stands for Plan-Do-Study-Adjust, a technique for methodically implementing and evaluating changes. Kaizen helps us break down a process operation in order to make it better. And heijunka teaches us to find ways to level-load the process to smooth the workflow.
Remember to consider all sources of NVA when planning a new process, project, or service delivery, in order not to suboptimize on one or two at the expense of the others.
The difficulty of reducing or eliminating Waiting NVA depends greatly on how accustomed the people performing the process are with the status quo. Often, bad practices persist because they seem to work in spite of the presence of NVA.
Don’t let “It’s not NVA, it’s just the way it is” doom your Lean Six Sigma improvement efforts.
Dann Gustavson, PMP®, Lean Six-Sigma Black Belt, helps Program Managers and their teams achieve superior results through high-impact program execution. Prepare, structure, and run successful programs in product engineering, manufacturing operations (including outsourcing), and cross-functional change initiatives.
Contact Dann@Lean6SigmaPM.com.