Practical Lean Six Sigma Service Offerings
Bring the benefits of Lean Six Sigma PM to your business operation using Practical Lean Six Sigma (PL6s). The project management consulting services described below can be customized to your business needs.
Interim Project Manager
Planning to transition an internal PM to your newest strategic project after her current project closes? Or recruiting to add a new full-time Senior Project Manager?
As the Engineering, Operations, or PMO Executive, you have a few choices while you’re in the transition. You could act as the PM yourself, thus adding one more critical activity to fill your “idle hours.” You could delay the new project until you have transitioned or hired the PM you need. Or you could assign the new project to your planned internal PM before her current project closes, letting her figure out how to put full attention on two critical projects without jeopardizing either one.
Obviously, none of these choices are good for your organization’s performance.
Here’s an alternative that alleviates those problems for you. Bring me in temporarily as your Interim PM while you go through the hiring and selection process, or the transition for your internal PM. I will keep the project moving for you, and will introduce appropriate Lean Six Sigma PM project techniques to team members when opportunities arise.
Interim duration as needed, with 2-3 week overlap and handoff to your full-time PM when available.
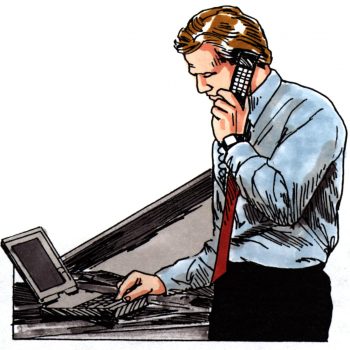
Bringing in a short-term Interim PM can help keep multiple projects moving while not stretching existing team members too thin, and keeping long-term resources aligned with business needs.
Your Hot New Project - Prepare, Plan, and Kickoff for Over the Top Success
You have high expectations for your newest project. You need it to succeed, however, the timeline is short. Don’t skimp on the planning and kickoff!
Quick story. It was my first day at a new company. They hired me to manage a new product introduction engineering project already underway. I dealt with all of the HR paperwork in the morning and got my badge (#1463).
After lunch, I stopped by the office of the manager running another similar project, and who my VP told me was the caretaker of my project while awaiting my arrival. We exchanged pleasantries, and then getting down to business and eager to accept the handoff, I said, “So, what’s the game plan, Henry?”
His answer floored me. He looked at me with a stern expression and said brusquely, “There’s no TIME to PLAN! It’s just bust our @&&^$s twenty-four-seven until we’re done!!”
Net, the project had supposedly been underway for two months, yet with Henry as acting PM (in name only) nothing was happening. Fortunately, it was not my first rodeo; by the time I went home Monday evening, I had met my team members and heard their perspectives, I had a plan for a plan, and from Tuesday onward my team was making progress.
Don’t you be like my friend Henry.
Indeed there is time to plan, and a few days wisely spent getting things right before the ‘kickoff’ can save weeks of difficult problem-solving later on. There are some fundamentals that have to be included in every project plan. Plus, there are a few low-effort, high-impact enhancements (inspired by Lean Six Sigma) that can make the difference between ‘Success’ and ‘Over the Top Extraordinary Success.’
In my humble opinion, you want Over the Top Extraordinary if at all possible. So does your senior management team. That’s where I can help. You don’t need to experience the common pitfalls during project execution — pitfalls that are often the result of poorly defined goals and scope, or one uninformed decision, or an unidentified risk, or an ill-advised shortcut, or an unwise action by a well-meaning stakeholder.
Here’s some sage advice for you.
Learn from other people’s mistakes;
you can’t live long enough to make them all yourself.
That advice comes not from a seasoned Program Manager with a string of credentials and certifications. It’s from former first lady Eleanor Roosevelt.
Ping me, set up a brief telecon to discuss your upcoming project or program, and we can go from there. Go for Extraordinary!
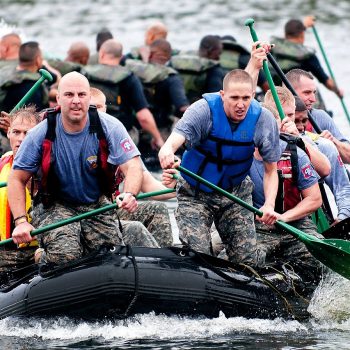
Don’t settle for a project completion that is just good enough. Put the extra effort into planning, preparation, and kickoff. Inspire your team to achieve the highest level of business performance. Lean Six Sigma techniques can make the difference.
Agile Kaizen Leader
Are you considering several initiatives for improving delivery times and quality for your business unit, but grappling with how to fit additional projects into your team’s already full workload?
Agile Kaizen is one of the Lean Six Sigma PM methodologies used for just that purpose. Here’s how it can help you.
We will define and prioritize your processes that could benefit from a kaizen improvement. The Japanese term ‘kaizen’ means simply “break down to make better.” Agile project management techniques work well in small kaizen teams, with minimal intrusion on existing work requirements.
Taken together, Agile + Kaizen results in step improvements to problems addressed sequentially, with minimal disruption to your team’s ongoing customer and internal commitments.
We will evaluate your business unit’s problem set – quickly! – then select the most beneficial starting project and appoint your team; they will thoroughly learn the agile kaizen methodology by executing the project.
Using the Plan-Do-Study-Adjust (P-D-S-A) framework and selected Agile PM methods, we’ll set up and conduct the kaizen, and publish a full report with ROI analysis and follow-up planning for further improvement opportunities. Your kaizen team will be able to apply their experience to conduct those future kaizen initiatives on their own or with minimal external support.
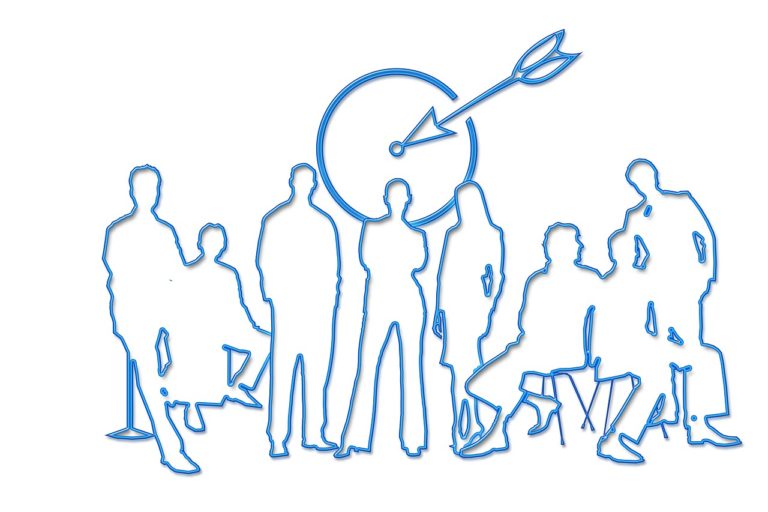
The Agile Kaizen team selects a process for their improvement focus, measures the current state, sets a stretch goal for improvement, then takes daily steps using the Lean P-D-S-A framework to move toward a solution and methods of control.
Project Schedule Flashing Yellow and RED? Build an Action Plan to GREEN!
You’re several months into a one-year-plus business-critical project, and you realize that the next major milestone date will slip – BIG! Maybe there are multiple indicators showing RED; it is not immediately clear what the problems are, nor how the lost time can be made up.
Senior management expects the end date to be met, if not improved. The revenue and margin impact of being late are unacceptable.
Don’t throw in the towel yet, and Don’t sound the alarm to your VP or CEO yet, either. Instead, Do be proactive, and Do begin with the end in mind.
You’ve heard this before –
Never bring problems to the executive team. Bring solutions.
Ping me, let’s talk – I can help you get moving toward your solution, and getting your schedule back to GREEN. Although there are no cookbook answers, there are LSS, CI, and OpEx tools that we can use to devise creative solutions to most project schedule problems. I will collaborate with you and your project team to address and take action on the problems, concerns, and issues. We will identify the underlying causes and plan valid countermeasures.
In short, we will develop your “Action Plan to GREEN” that gets future milestones and the project’s End Date back where they need to be. Oh! – and put forward-looking project controls in place to make sure you’re not surprised again in a few weeks.
In the process of doing so, you will have enhanced your team problem-solving capability so that you can handle issues on this and future projects, if not always with ease, then at least without panic.

If it’s looking like a schedule slip is about to happen, don’t get stressed. Shift gears and get to work on the action plan that will get your project back on track – back to Green.
Facilitated After Action Review (End-of-project)
Does this sound familiar? Your recently completed project experienced some successes you would like to replicate, and some challenges you would like to avoid in the future. I call these “Went Well” and “Went Poorly.” Both categories of experience are important to understand and learn from.
The Lean Six Sigma P-D-S-A approach provides a good framework for capturing the project experience for future PM and team education.
I will facilitate a thorough After Action Review with the project team members including sponsor or PMO, to ensure a deep understanding of the root causes of successes and setbacks. We’ll develop actions to replicate the causes of successes and correct the root causes of setbacks for future projects.
We’ll identify opportunities to improve future projects by applying Lean Six Sigma (LSS) techniques, and the requisite learning to enable the team to use LSS effectively.
In addition to a report of the objective evidence, we’ll develop a Case Study in a format that facilitates training your next wave of PMs and core teams, thereby improving your organization’s bench strength.
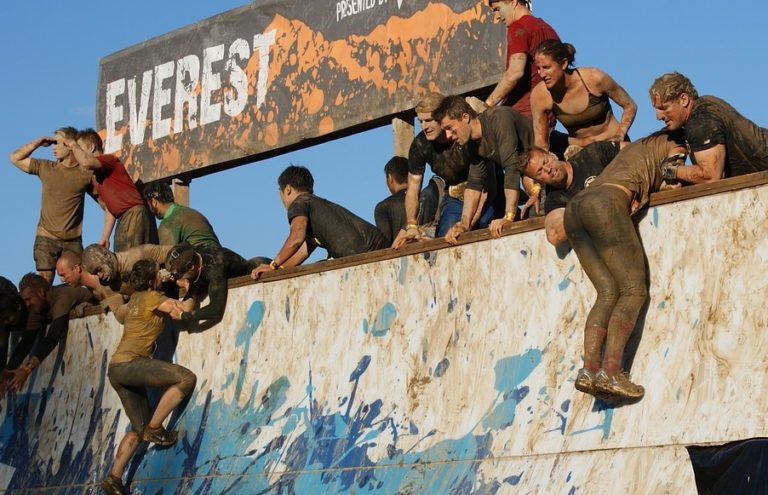
Your difficult project is in its closeout stage. By conducting an After Action Review, you will review and critique the process your team went through, in order to understand the causes of your successes and setbacks. In that way, continuous improvement can be applied to your execution of future projects.
Focused Lean Six Sigma PM Education
Many professional association and university Project Management and Lean Six Sigma (LSS) training programs are a great long-term investment in staff development.
One down-side, though, is they take your high performers out of the workplace for several weeks to learn the full suite of PM and LSS tools and techniques, most of which may not apply in your business.
My alternative pulls your project and program managers, plus your potential LSS Black Belt candidates, into a Learn While Doing initiative customized to your business unit’s most pressing needs.
We will cover the vital few Lean Six Sigma PM tools and techniques that apply to your project work currently in progress.
The “Dynamic Dozen.”
We’ll address the “live” problems your project teams are facing, and they will develop and implement solutions in a LSS context.
The initiative structure is customized to suit your business needs. Early morning, late afternoon, or other minimally-intrusive time schedule.
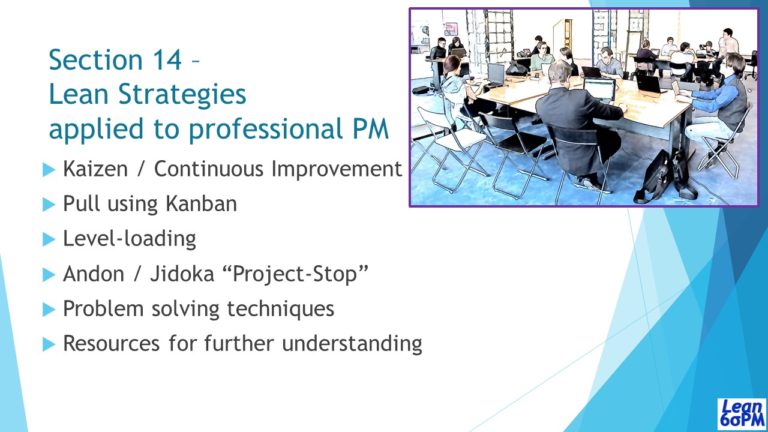
Your project team and LSS belt candidates participate in focused education in the disciplines of lean, six sigma, and professional project management. The Learn While Doing approach consists of presentation, discussion, and hands-on experience applied to their actual project work in real time.
The initiatives on this page provide an idea of the tools and techniques that can be applied to your organization using the Practical Lean Six Sigma (PL6s) approach. Any of these can be customized to suit your needs, or you can contact me to discuss your environment, problems, and goals. Then together we can develop an approach that meets your needs and budget.
Contact me to discuss how to apply Practical Lean Six Sigma to your business challenges.
Email: Dann@Lean6SigmaPM.com.